Variable Frequency Drives (VFDs) have revolutionized industrial power management by fine-tuning motor speeds, slashing energy costs, and prolonging equipment life. Every industry—from manufacturing to HVAC—benefits from VFDs’ adaptability, with load profiles tailored to specific operational needs. When coupled with specialized filters like MTE’s Matrix AP filters, VFDs provide even greater performance, particularly at lighter loads where energy consumption can add up over time. Let’s look at how these technologies perform across industries, with a deeper dive into a real-world application.
Why Industries Are Turning to VFDs for Energy Savings
Each industry has unique needs for VFDs. For manufacturing, VFDs regulate the pace of heavy machinery and conveyor systems, typically operating between 30-90% capacity to match production demands. In HVAC, where fans and pumps don’t require constant full-throttle operation, VFDs operate at 30-70% capacity, enhancing energy efficiency and reducing wear on equipment during off-peak periods.
Water treatment plants rely on VFDs for precise control of pumps and blowers, which vary based on water usage, with load profiles usually between 50-85% capacity. For mining and extraction, VFDs power drills and pumps, adapting to the rugged demands of extraction while reducing power during low-demand intervals.
Elevating Performance at Light Loads with MTE Matrix AP Filters
Many industrial processes run the bulk of their time at lighter loads, especially in HVAC systems and manufacturing where equipment is rarely pushed to full capacity. This is where MTE Matrix AP filters provide a critical advantage, performing optimally at 30-100% capacity. The Matrix AP Filters outperform other passive harmonic filters at lighter loads. This reduction in harmonic distortion across varying loads translates into IEEE-519 Compliance and tangible savings, especially in sectors where these lower loads constitute the majority of operational time.
Case Study: Replacement of Damper Controls with VFDs in an HVAC System
Company Background
A textile processing plant specializing in raw fiber processing needed a solution to improve the energy efficiency of its HVAC system. Operating around the clock, the facility sought to enhance air quality and reduce energy costs for its workers. Working with a VFD specialist, the company retrofitted 15 of its HVAC system’s 18 fan motors with VFDs, aiming to optimize ventilation without sacrificing air quality.
Project Overview
The plant’s ventilation relied on a network of nine supply fans and nine return fans, controlling airflow and filtering particulate matter from the processing area. Initially, airflow was controlled using damper mechanisms, which were inefficient and required manual adjustments. To monitor performance, system data was collected over two weeks, capturing motor power, damper positions, and fan power. This baseline data was used to assess the energy demand and create a load profile for both peak and off-peak periods.
Implementation and Results
After determining that the ventilation system fans were oversized, the team installed VFDs on 15 of the 18 fans, leaving only those that needed to run at full capacity. By retrofitting these fans with VFDs, the plant could fully open its dampers and adjust fan speed dynamically. This adjustment allowed the facility to reduce its ventilation system’s electricity demand from around 322 kW to 133 kW—a substantial 59% reduction. The total energy usage of the system dropped from 2,700,000 kWh to 1,100,000 kWh annually, leading to yearly energy cost savings of approximately $101,000.
Financials and Payback
The retrofit project cost $130,000, which included feasibility studies, engineering, equipment, installation, and measurement and verification activities. With annual savings of $101,000, the plant expects a simple payback period of just 1.3 years. The energy efficiency gains made possible by the VFDs eliminated the need for damper adjustments, reducing labor and enhancing control over the ventilation system.
Project Cost | $130,000 |
Annual Energy Cost Savings | $101,000 |
Simple Payback | 1.3 years |
Demand Savings | 189 kW |
Annual Energy Savings | 1,579,400 kWh |
This case study illustrates how VFDs, paired with intelligent system adjustments, can generate meaningful savings. With this setup, the textile plant achieved better control, energy reduction, and air quality for employees—all while recouping the project cost within a short period.
Source: https://natural-resources.canada.ca/energy-efficiency/energy-star-canada/about/energy-star-announcements/publications/variable-frequency-drives/15362#a1f
Driving Superior Harmonic Mitigation and Energy Savings
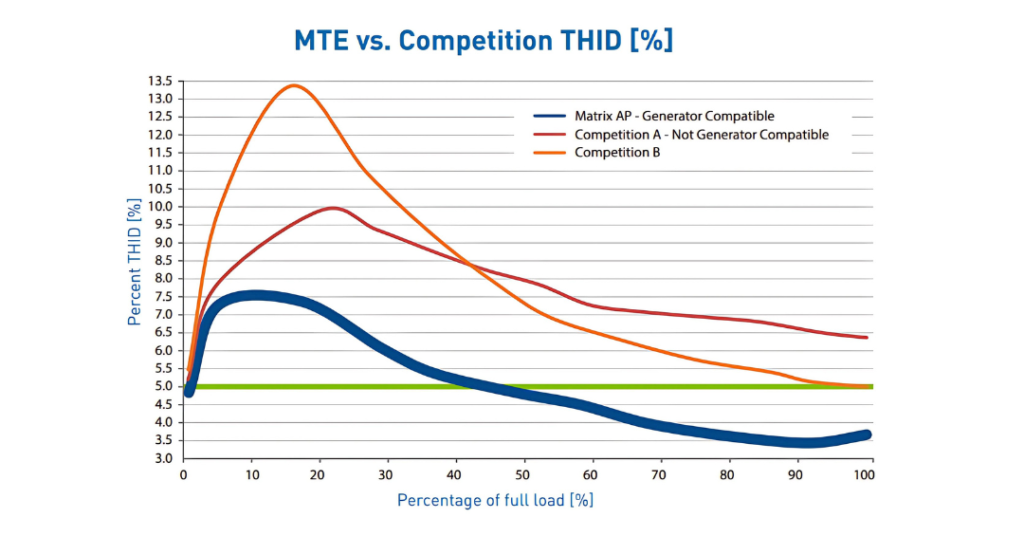
Throughout this article, we’ve explored how VFDs enable facilities to fine-tune energy usage, prolong equipment life, and achieve substantial cost savings across various industries. But the true potential of these systems is only fully realized when they’re paired with the right harmonic filtering solution. The MTE’s Matrix AP (Adaptive Passive) filter is a critical complement to VFDs that ensures consistent efficiency and equipment protection.
While traditional passive filters tend to falter at lighter loads, where much of industrial operation takes place, MTE’s Matrix AP filters are designed to thrive. Unlike competitor products that can hit the 5% harmonic target only at full load, MTE’s Matrix AP filters achieve remarkable harmonic mitigation even at 30-60% capacity. This consistency is invaluable in industries like HVAC and manufacturing, where equipment rarely operates at peak load. By maintaining optimal harmonic reduction across varying load profiles, MTE’s Matrix AP filters prevent electrical waste, reduce motor overheating, and ultimately save on energy costs—especially when lighter loads dominate operations.
Your system adapts to varying conditions, and your harmonic filter should too. MTE’s Matrix AP filters ensure your VFD-powered systems reach their full potential in terms of efficiency and longevity. For facilities seeking a powerful approach to sustainable power management, MTE’s Matrix AP filters are a vital investment that enhances system resilience and amplifies energy savings.
Available at Vanco Electrical Solutions – Certified Distributor of MTE